I have wanted projects to play with some of the newer machine learning algorithms for a while, so this year’s holiday hacking project is going to be an autonomous underwater drone (AUV). The plan is to start by designing the ballast system first, as it can be independently tested and as a module.
From what I understand Navy Subs use compressed air, charged during surface stops, to run their ballast systems. Water is driven out of the ballast chamber by opening valves on the bottom of the ballast tank while leaking high-pressure air into the chamber. Similarly water is let into the ballast chamber by opening the valves on both the bottom and the top of the ballast tank, letting air escape out the top while water enters through the valves at the bottom of the tank.
I am thinking of using a similar approach for the first version of the AUV. The main difference is that rather than compressed air, I am going to try using CO2. So something like this – where there are two solenoid valves for air and water venting to a ballast tank, and a third valve and regulator system for letting CO2 into the ballast tank.
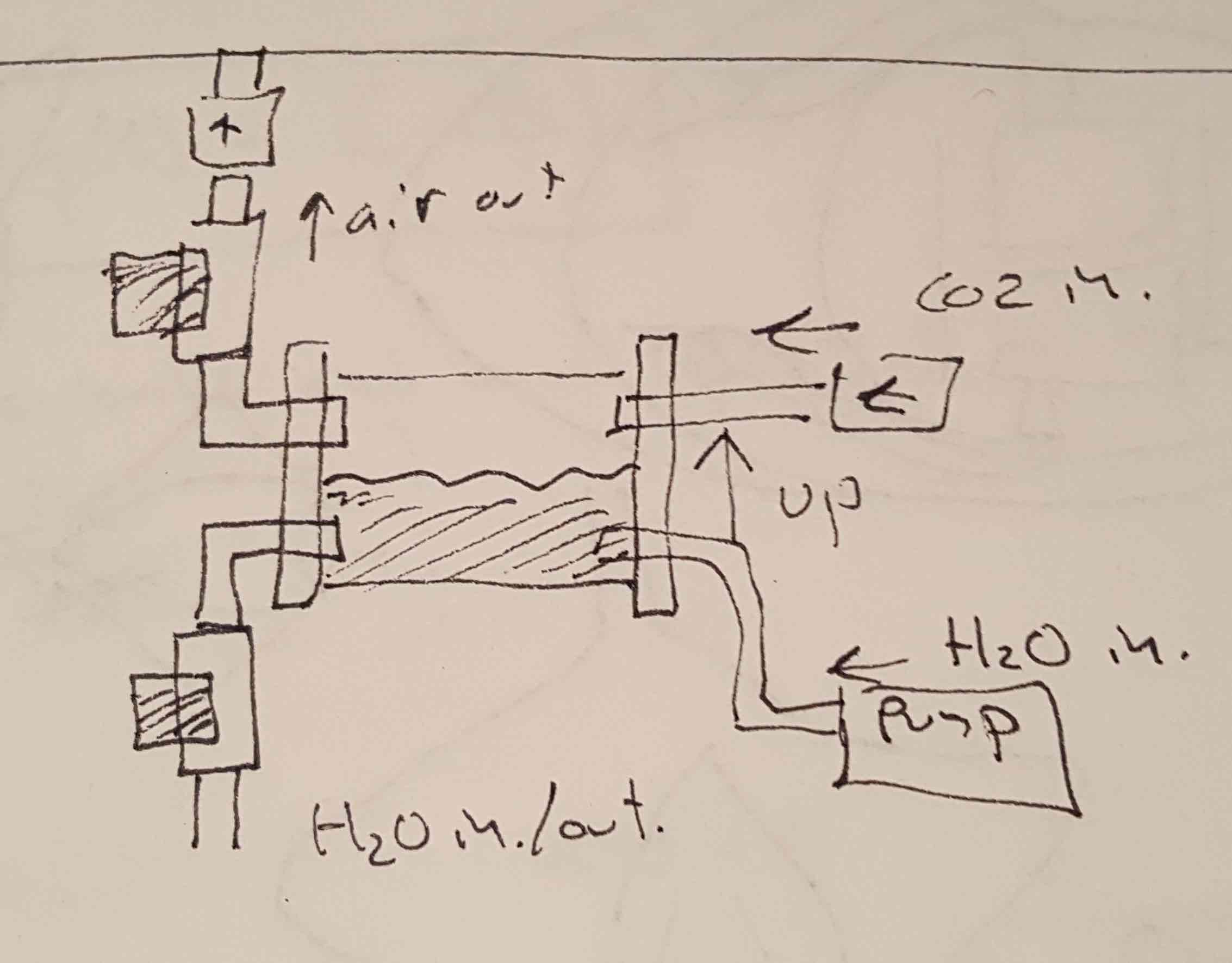
So to empty the ballast tank with this system you open the valve to the water, at the bottom of the tank, and then blast in CO2.
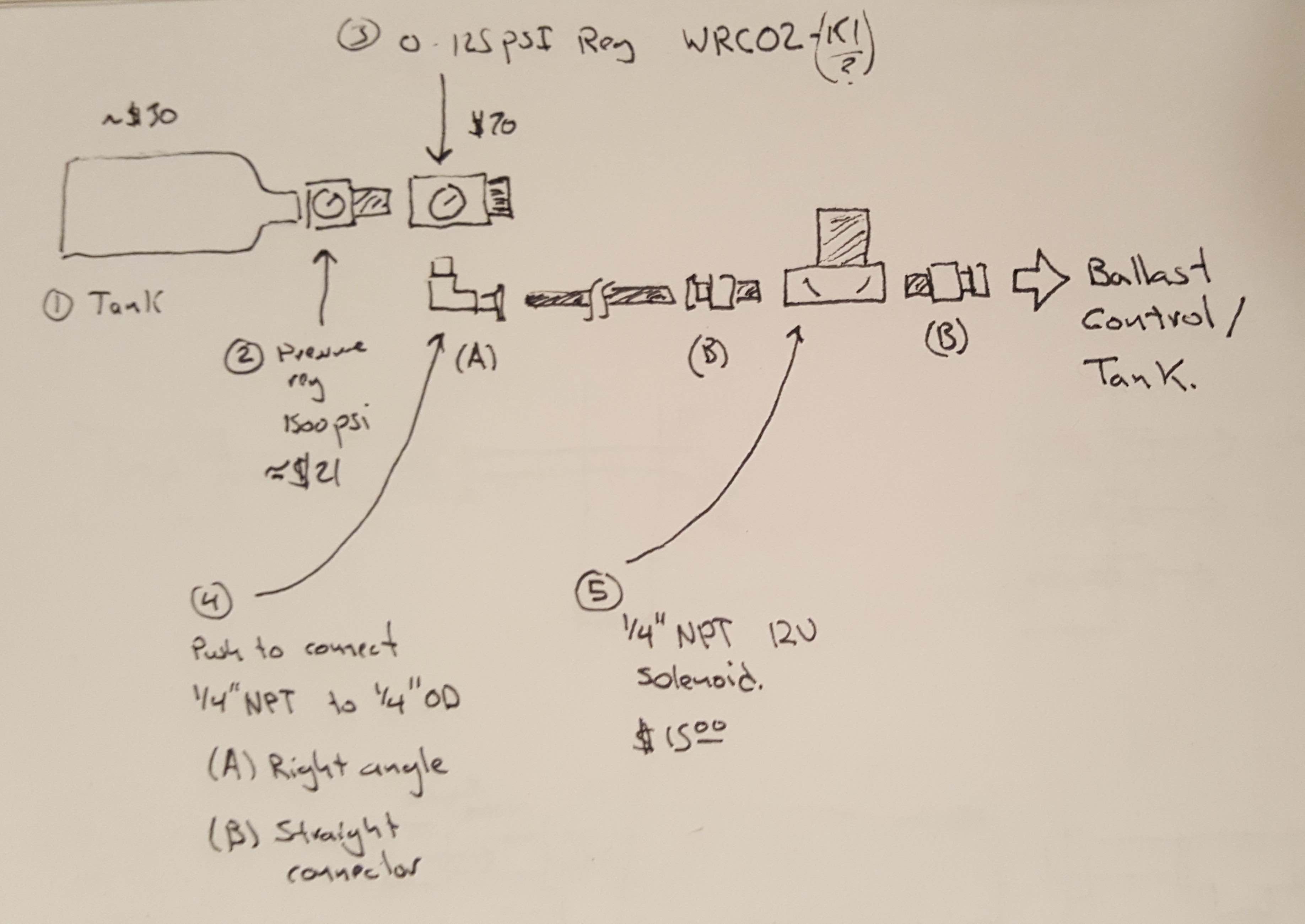
For the CO2 side of things version one will use a pressure regulator intended for hooking CO2 tanks to compressed air tools. They are relatively cheap 80-160PSI regulators. For plumbing I am going to use 1/4 inch NPT push to connect fittings and pressure line meant for breaks. The design adds an on off valve to the tank as a safety for when the AUV is being transported. Best guess is $140 for ballast control.