Started printing this version, which prints both the hook and the dart body. Problem with that is the printed dart body does not work with the compressed air spring driven Nerf guns or the electric Nerf guns dart accelerators. It was kind of a disappointment for my nephew.
http://www.thingiverse.com/thing:360571
My nephew and I did find this version of the grapping hook. It required cutting up a Nerf dart, but it worked amazingly well. It was also fast to print.
http://www.thingiverse.com/thing:604853
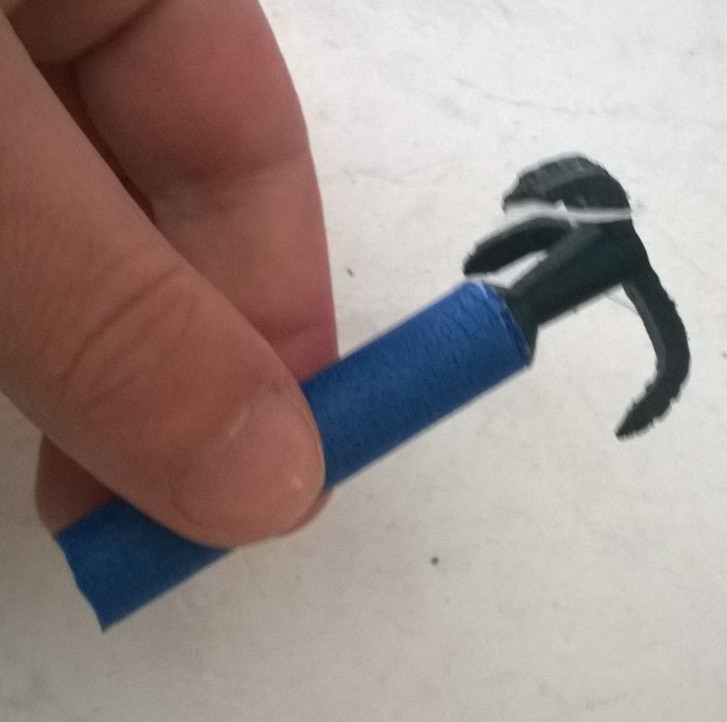
We bought a Nerf Jolt to use to launch the darts. Amazon has them for $6, and it works perfectly with the grappling hook dart. They also sell them in groups of 4, which would let parents and adults watching kids to stash them around the house. You know, in case you wanted to retaliate to any surprise Nerf attacks.
After we made the grappling hook, we designed and printed up a modification to the Nerf scope we designed so it clipped onto the Jolt. My nephew did the design and used calipers to take the needed measurements, and I did some translation into Solidworks for him.
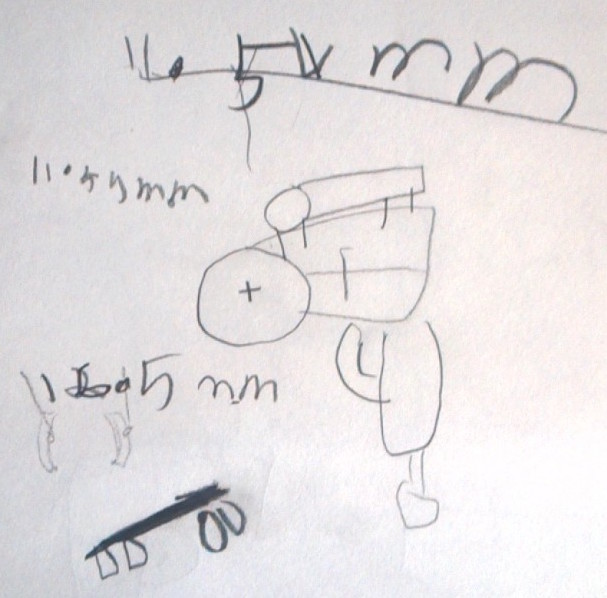
With printers, VR, and AR all taking off someone seriously needs to make a decent CAD package targeted at kids. My nephew is a pretty impressive kid, but I was still surprised by how he walked through designing his scope. This was actually the second scope we built, so I’ll talk about his designing in another post, but I was impressed. He iterated a bunch of really specific designs on paper before telling me exactly what he wanted his scope to look like. He even tried out different lollipop and crosshair designs.
For “rope” we used a 15 foot section of dentil floss. Use the un-waxed type if you have a choice, it helps keep it from knotting. I added a front cross bar and spars to hold the “rope” on the grappling hook. Firing the dart would cause the “rope” to unspool as the dart flew, and winding up the rope kept it from getting tangled when not in use. Still, using the spars also meant that the kid firing the grappling hook had to re-wind after every shot. So I think I should have not added anything to my nephews design. It did provided an opportunity teach him what feature creep on a spec was, and that it is not your friend.
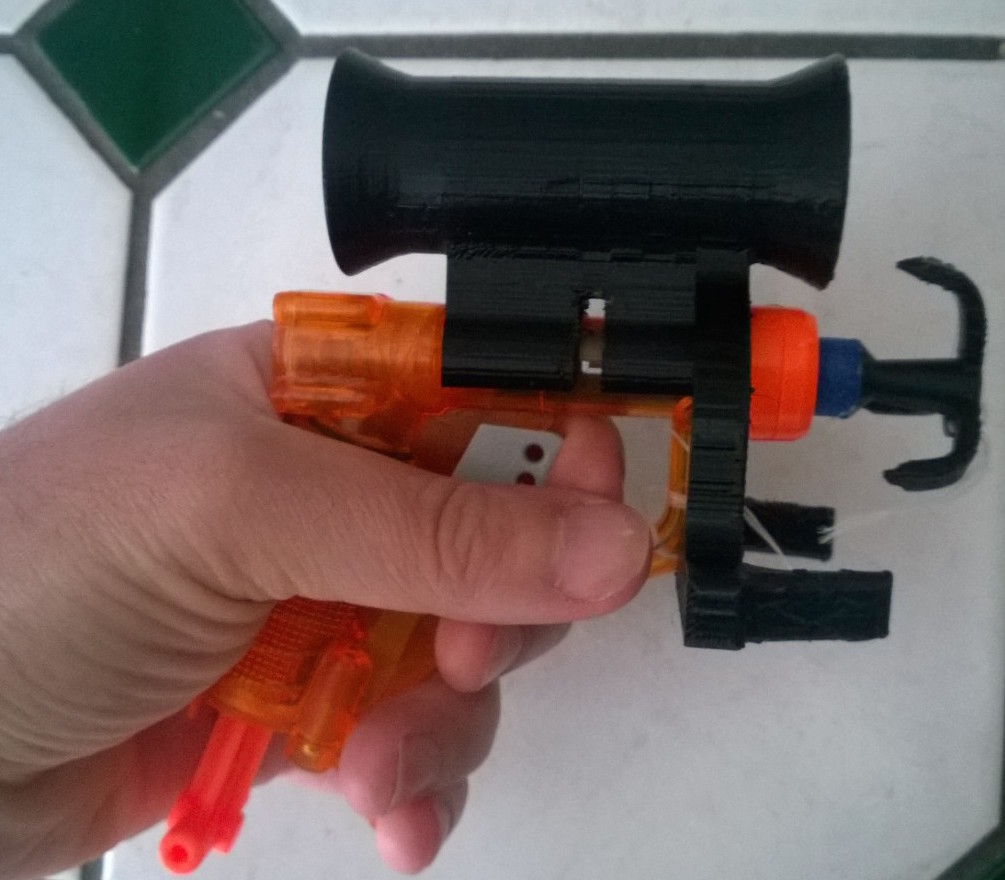
All in all we spent a good hour playing with the grappling hook, launching it at different things and trying to reel them in. The calipers we used to take measurement were also a bit of a hit in their own right. In retrospect though I would wait until the child in question was 9-10. The CAD modeling takes a good while even if you are keeping things simple and attention spans can begin to get exceeded.